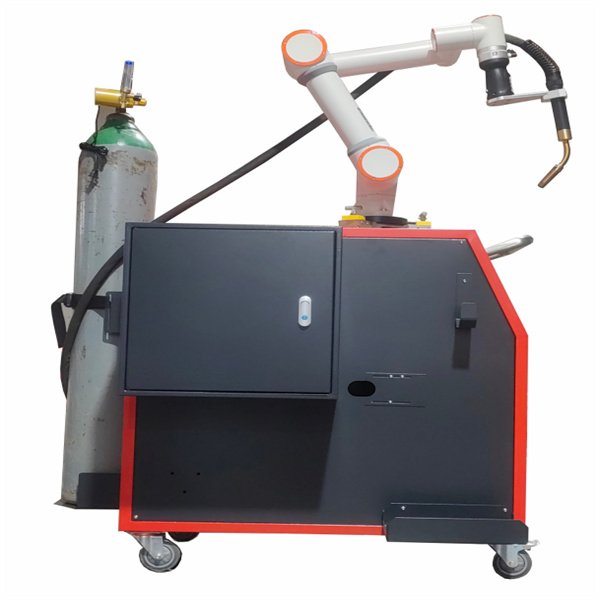
How Do Automated Welding Robots Improve Welding Quality?
In modern manufacturing, the demand for precision, consistency, and speed has pushed industries to embrace automation. One of the most significant advancements in manufacturing technology is the introduction of automated welding robots. These intelligent machines are transforming welding operations by providing high-quality results, reducing human error, and boosting overall productivity.
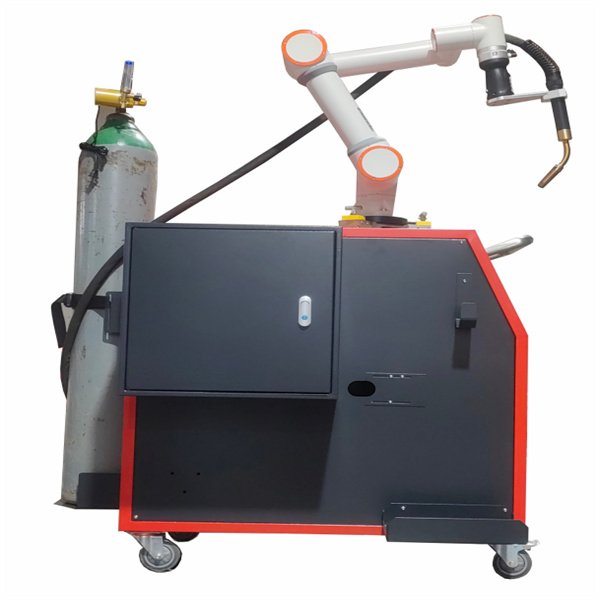
How Automated Welding Robots Improve Welding Quality
1. Precision and Consistency
One of the main advantages of automated welding robots is their ability to perform welding with a high degree of precision. Robots are programmed to follow specific paths, ensuring that the welding process is uniform and consistent from start to finish. This eliminates the risk of human error, such as inconsistent welding speeds or incorrect torch angles, which can lead to defects and weakened joints.
In manual welding, slight variations in technique can significantly impact the final product. A skilled welder may have more control over the process, but fatigue, distractions, and other factors can affect the quality. Automated robotic welding systems, on the other hand, follow pre-programmed instructions, ensuring each weld is executed with the same level of precision every time. This results in welds that are stronger, cleaner, and more durable.
2. Repeatability
Repeatability is crucial in any manufacturing process, particularly when producing high volumes of parts. Automated welding robots excel at repeatability, consistently delivering the same high-quality welds in each cycle. Since robots use the same settings, parameters, and movements each time, manufacturers can ensure that every product produced on the production line meets the same high standards.
For industries that require large-scale production, such as automotive manufacturing, this repeatability is essential. It not only reduces the chance of defects but also ensures that each component is welded to the same specifications, which is critical for the overall quality and safety of the final product.
3. Improved Weld Strength
Weld strength is vital in ensuring that welded joints can withstand stress and pressure without failing. Automated welding robots help improve weld strength by maintaining a consistent heat input during the welding process. Robots are programmed to control the speed, angle, and pressure of the weld, which optimizes the heat distribution and minimizes the risk of weak spots.
In manual welding, variations in heat distribution can lead to weak welds, creating areas that are prone to cracking or breaking under pressure. With robots, these inconsistencies are eliminated, resulting in stronger, more reliable welds that meet rigorous quality standards.
4. Enhanced Heat Control
Proper heat management is crucial for achieving optimal welding results. Automated welding robots are equipped with advanced sensors and software that allow them to monitor and control the heat during the welding process. This ensures that the metal is heated uniformly, preventing overheating or underheating, which can cause defects such as warping, cracking, or inadequate fusion.
By maintaining optimal heat levels, automated welding robots ensure that the welding material bonds properly and creates a smooth, consistent joint. This level of control is difficult to achieve with manual welding, where heat control largely depends on the welder’s skill and experience.
5. Reduction of Contaminants
Contaminants such as dust, oil, or moisture can negatively affect the quality of a weld. When a welder manually applies the welding process, there is always a risk of contaminants being present on the workpiece. Automated welding robots, however, are able to work in controlled environments, reducing the exposure of the workpiece to potential contaminants.
Additionally, the use of automated systems allows for more efficient cleaning of workpieces before welding, ensuring that the surfaces are free from foreign materials. This results in cleaner, higher-quality welds, as contaminants are less likely to interfere with the fusion of the metal.
6. Reduced Distortion
Welding can often cause the metal to warp or distort due to uneven heat distribution. Automated welding robots help mitigate this issue by carefully controlling the welding parameters, including heat, speed, and the angle of the welding torch. By maintaining precise control over the welding process, robots reduce the amount of heat applied to the workpiece, preventing excessive distortion.
This is especially important for industries where part geometry and tolerances are critical, such as aerospace and automotive manufacturing. Automated welding robots can maintain tight tolerances, ensuring that parts fit together as intended and reducing the need for post-weld corrections.
Why Choose an Automated Robotic Welding System?
The choice of an automated robotic welding system plays a significant role in ensuring the success of welding operations. These systems are designed to handle complex welding tasks with greater precision and reliability than traditional methods. When selecting an automated robotic welding manufacturer, companies should consider factors such as:
1. Customization:
Many automated welding robots can be customized to meet specific needs, such as the type of welding (MIG, TIG, etc.), the size of the workpieces, and the complexity of the welding task. An experienced automated robotic welding manufacturer can provide tailored solutions that maximize efficiency and quality.
2. Support and Maintenance:
Choosing a manufacturer that offers comprehensive support and maintenance services is critical. Regular maintenance ensures that the robots continue to operate at peak performance, minimizing downtime and maintaining high-quality output.
3. Integration Capabilities:
The ability to integrate the robotic welding system with existing production lines is essential for a smooth transition to automation. A reliable automated welding robots supplier will offer solutions that can easily integrate with your current operations, reducing the learning curve and ensuring minimal disruption.
Conclusion
Automated welding robots are revolutionizing welding processes by improving welding quality, consistency, and efficiency. With their precision, repeatability, and enhanced heat control, these robots are transforming industries by ensuring stronger, more reliable welds. By reducing the chances of human error and improving the overall welding process, automated welding robots are becoming indispensable in sectors such as automotive, aerospace, and construction.
For businesses looking to improve their welding operations, investing in automated robotic welding systems is a smart move. These systems not only enhance the quality of the welds but also increase production efficiency, reduce costs, and ensure safety in the workplace. With a trusted automated robotic welding manufacturer, companies can optimize their welding processes and stay competitive in the ever-evolving manufacturing landscape.