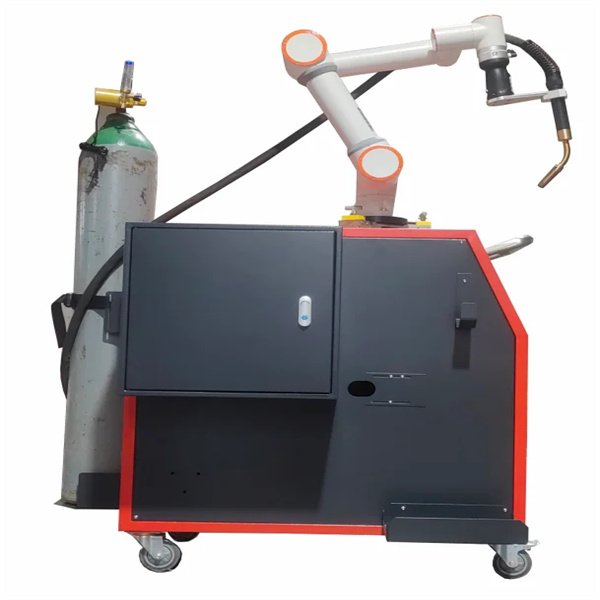
How to Operate an Automated Welding Robot
In the world of industrial automation, automated robotic welding has become a cornerstone for improving productivity, consistency, and safety in manufacturing processes. Welding robots are designed to execute precise and repetitive welding tasks with minimal human intervention, ensuring efficiency and quality in production lines. But for businesses looking to integrate this technology, understanding how to operate an automated welding robot is essential.
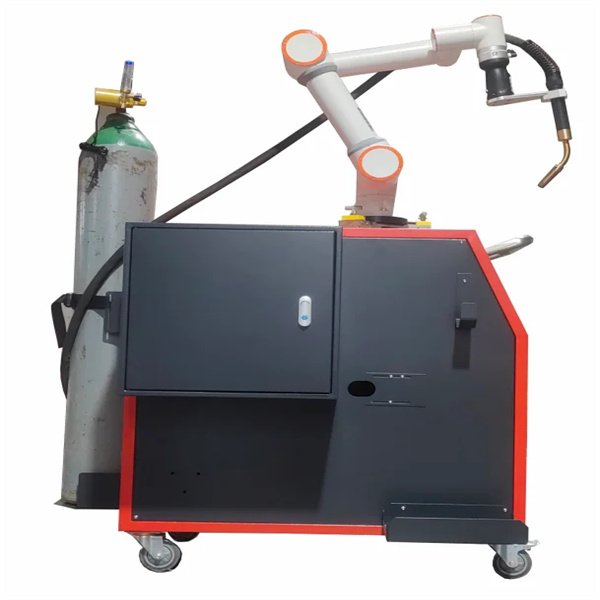
Steps to Operate an Automated Welding Robot
Operating an automated welding robot involves several stages, from setup to execution and maintenance. Below is a step-by-step guide:
1. Preparation and Setup
Before starting the welding process, proper preparation is crucial. This includes:
Workstation Setup: Ensure the welding workstation is equipped with all necessary tools, including the welding robot, power supply, and safety equipment.
Material Preparation: Clean and prepare the materials to be welded. Remove any dirt, rust, or grease from the surface to ensure a strong and clean weld.
Robot Calibration: Calibrate the robot to ensure its movements and welding parameters align with the task requirements. Proper calibration is critical for achieving precision and consistency.
2. Programming the Welding Robot
The robot must be programmed to perform the welding task. This involves:
Defining the Welding Path: Use software to define the welding path, speed, and orientation. Many modern welding robots allow operators to use drag-and-drop interfaces or physically guide the robot arm along the desired path.
Setting Parameters: Configure parameters such as welding voltage, current, and speed. These settings depend on the type of material, weld type, and thickness.
Testing the Program: Run a trial program to ensure the robot performs the desired movements correctly. Make adjustments as needed to optimize accuracy.
3. Safety Checks
Safety is a top priority when operating any robotic system. Before starting the welding process, perform the following checks:
Ensure all safety guards and barriers are in place.
Verify that emergency stop buttons and safety sensors are functional.
Equip workers with appropriate personal protective equipment (PPE), such as gloves, helmets, and goggles.
4. Executing the Welding Task
Once everything is set up, you can begin the welding process:
Start the Program: Activate the robot and begin the pre-programmed welding task.
Monitor the Process: Observe the robot’s operation to ensure it follows the programmed path and parameters. Address any issues immediately to prevent errors or defects.
Inspect the Weld: After the welding process, inspect the welds for quality and consistency. Use tools like weld gauges or X-ray inspection systems for thorough analysis.
5. Maintenance and Troubleshooting
Proper maintenance is essential to keep the welding robot functioning optimally. Regularly:
Clean the robot and welding tools to remove debris and spatter.
Check for wear and tear on components such as nozzles, cables, and sensors.
Update the robot’s software and re-calibrate as needed.
Troubleshoot any errors or malfunctions with the help of your automated welding robot manufacturers or technical support team.
Tips for Optimizing Robot Performance
To get the most out of your welding robot, consider these optimization tips:
1. Use High-Quality Equipment:
Investing in the best automated welding robot ensures long-term reliability and performance.
2. Train Your Team:
Provide thorough training for operators to understand the robot’s capabilities, software, and safety protocols.
3. Optimize Programming:
Continuously refine your robot’s programming to improve speed and accuracy.
4. Collaborate with Manufacturers:
Partnering with reputable automated welding robot manufacturers gives you access to technical support, maintenance services, and upgrades.
Benefits of Using Automated Robotic Welding
Integrating welding robots into your production process offers numerous benefits, including:
1. Enhanced Productivity
Robots can work continuously without breaks, significantly increasing production rates and meeting tight deadlines.
2. Improved Quality
Robots deliver consistent and precise welds, reducing defects and rework.
3. Cost Savings
While the initial investment in a welding robot may be high, the long-term savings in labor costs, material waste, and downtime make it a cost-effective solution.
4. Workplace Safety
By automating welding tasks, workers are removed from hazardous environments, minimizing the risk of injury.
Selecting the Best Automated Welding Robot
When choosing the best automated welding robot, consider the following factors:
1. Application Requirements:
Identify the welding tasks you need the robot to perform, such as arc welding, spot welding, or TIG welding.
2. Payload and Reach:
Ensure the robot can handle the weight and size of the materials you work with.
3. Ease of Programming:
Look for robots with user-friendly interfaces and advanced programming capabilities.
4. Durability and Reliability:
Choose a robot built with high-quality components for long-term use.
5. Support Services:
Work with trusted automated welding robot manufacturers who provide installation, training, and maintenance services.
Conclusion
Operating an automated robotic welding system may seem complex, but with proper preparation, programming, and maintenance, businesses can unlock its full potential. From improving productivity and precision to enhancing workplace safety, welding robots offer unparalleled advantages in modern manufacturing.
To ensure the best results, invest in the best automated welding robot for your application and collaborate with trusted automated welding robot manufacturers who can provide expert support and guidance. With the right tools and knowledge, automated robotic welding can transform your production processes and set your business on the path to long-term success.